WARREN THREAD ROLLERS: DURABLE, DEPENDABLE, AND EASY TO USE
Warren thread rollers are the most technologically advanced, user-friendly, durable, and dependable thread rollers on the market today. Warren thread rollers offer unparalleled standard features and are available with a variety of optional components and equipment to meet your exact production requirements.
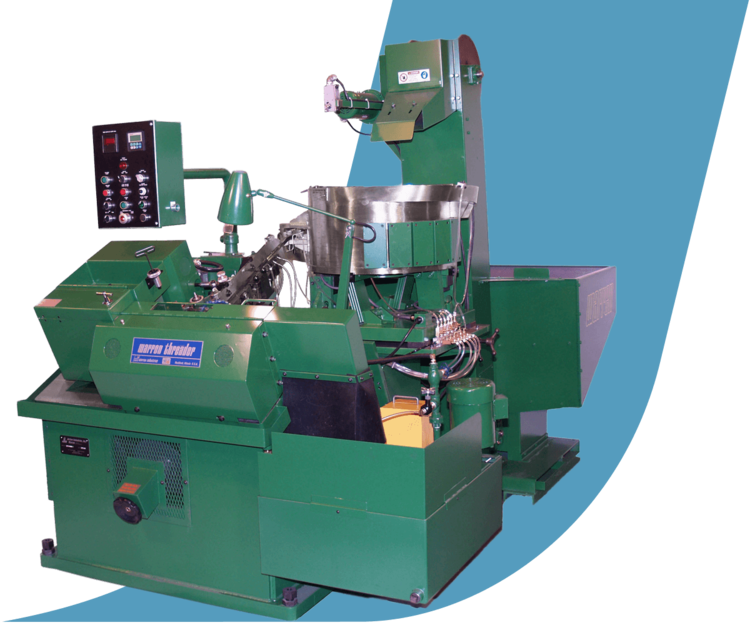
WE BUILD OUR THREAD ROLLERS TO MACHINE TOOL STANDARDS
They are designed for ease of operation and operator convenience, which means each thread roller features:
- Exclusive patented feed-stop/trigger system to ensure "skid free" starts
- Exclusive patented four-axis die adjustment and alignment system to ensure "lap free parts"
- Exclusive integral, ram mounted, pneumatic parts blow-off to ensure positive part discharge
- Exclusive feed rail height adjustment system
- NC variable speed drive to eliminate problems associated with sheaves, belts, and transmissions common on competitive system designs
- Heavy-duty ram and ram pocket that incorporates hardened steel wear plates on AMPCO bronze wear liners with an integral recirculating coolant system
- Integral high-pressure lubrication system to ensure consistent lubrication during operation
- Standard low-pressure shutoff to protect against plugged lubrication system
- Positive hydraulic lock-down of sub-plates on WT-10, 20, & 30 — Belleville washers on all other models
- WT-10, 20, & 30 includes hydraulic adjustment of feeder bowls
- Removable coolant tank that can be easily moved to a remote location for cleaning, which eliminates the problems and mess associated with integrated tanks
PATENTED FOUR-AXIS SETUP ADJUSTMENT: THE KEY TO LAP FREE PARTS
- Die Match: The bottom sub-plate allows adjustment of the first axis for die match. The bottom sub-plate is moved by an adjusting screw, which features an integral graduated dial for precise adjustment.
- Die Inclination (Finish Squeeze): The top two sub-plates provide adjustment for the second axis, which affects die inclination. Turning the adjusting screw causes the top two plates to position the leading edge of the stationary die. This adjustment determines the amount of penetration at the end of the rolling process.
- Die Squeeze: The third axis, which determines the die squeeze at the start of the rolling process, is accomplished by adjusting the position of the top sub-plate.
- Die Tilt (Optional): The fourth axis adjustment, mounted into the die tilt block, allows the die to be tilted for applications using tapered blanks.
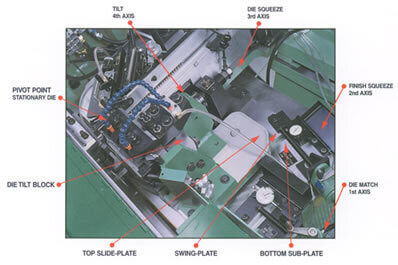
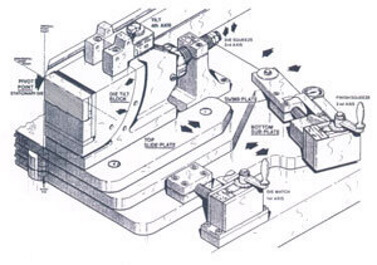
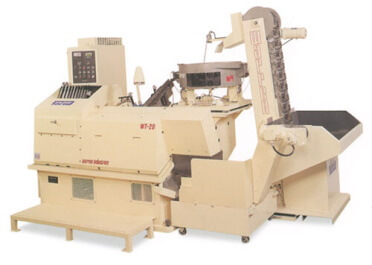
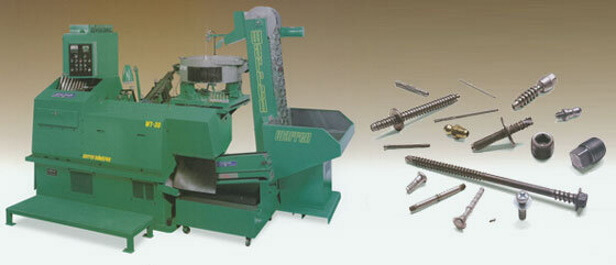
PATENTED FEED-STOP/TRIGGER SIMPLIFIES CHANGEOVER AND ELIMINATES PART ROLLBACK
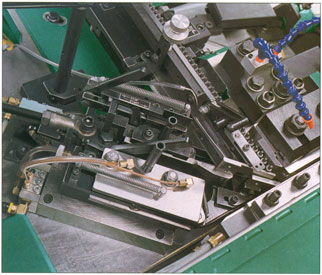
Warren thread rollers are equipped with our unique feed-stop/trigger design to prevent multiple blanks entering the die at the same time. The combination feed-stop/trigger system controls blank forces at the rail tip, ensuring that only one part at a time enters the die area. To eliminate the possibility of damage from "rollback" during high-speed operation, the swing-away keeper assures complete control and alignment of the blanks as they enter the die. Should a "rollback" occur, the swing-away keeper is designed to automatically retract, preventing damage to the tooling. By combining these features with the industry's most versatile pusher arrangement, the Warren thread roller offers unchallenged ease of setup and the industry's most user-friendly operation.
Another unique feature of all Warren thread rollers is the utilization of a 45-degree insertion angle. This exclusive design feature allows very high production speeds while maintaining absolute precision and blank control. As a result, Warren thread rollers eliminate "blank skid" during startup, which is common with other thread rollers.
STANDARD AND OPTIONAL THREAD ROLLER FEATURES
- Optional Spiral Thread Detection: "Spiral threads" or "run-ups" are caused by parts not starting straight in the rolling dies. The optional Warren spiral head detection system detects the parts that rise as they advance along the stationary rolling die. It then shuts off the machine.
- Feed Rail Features: Warren offers a feed rail design which increases operator efficiency, minimizes setup time, provides consistent feed control and precise part movement throughout the feed cycle.
- Blank Head Clearance Adjustment: (Standard) The exclusive "flip-top" rail system is designed using a specially designed adjustment mechanism which allows the operator to quickly and accurately adjust the blank head clearance at both ends of the feed rails.
- Clearing Jammed Feed Rail: (Standard) Warren's unique "breakaway" rail system design allows the operator to easily access and clear the feed rail in the event of a jam caused by an out-of-spec blank.
- Adjustable Rail Height: (Optional) The height of both rails can be adjusted simultaneously using a single control lever with integral locknut.
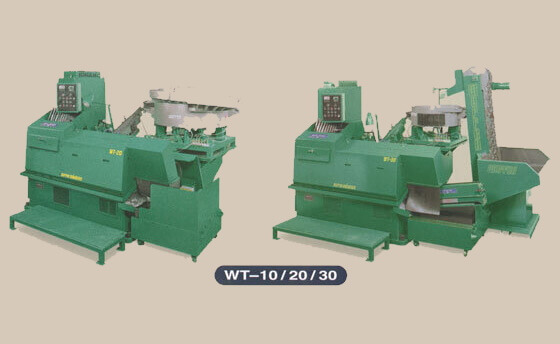
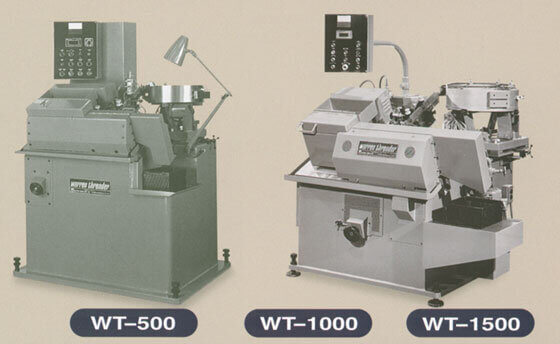
WARREN THREAD ROLLER SPECIFICATIONS
WT-500, WT-1000, WT-1500
WT-500
Die Requirement: "00" or "000"
Screw Dia. Capacity: #0000 to #6-32 (3.55)
Blank Length: inches (mm): 90 to 1-1/4" (31.75)
Speed Range: 150 to 1100 ppm
Die Pocket Depth: inches (mm): 1-1/8" (28.57)
Main Motor Drive: HP NC (kw): 2 HP A/C (1.4)
Electrical: 230 V/3PH/60 Cycles
Shipping Wt. Lbs. (kilos) (approx.): 2800 (1260)
Outline Dimensions
Height: inches (mm) 69" (1752.60)
Width: inches (mm): 36" (914.40)
Depth: inches (mm): 48" (1219.20)
Feeder-Stainless Steel (all vibratory): included
WT-1000
Die Requirement: "00" or "000"
Screw Dia. Capacity: #2 to #12 (5.49)
Blank Length: inches (mm): Up to 3" (76.20)
Speed Range: 90 to 1000 ppm
Die Pocket Depth: inches (mm): 3" (76.20)
Main Motor Drive: HP NC (kw): 7-1/2 HP NC (5.25)
Electrical: 230 V/3PH/60 Cycles
Shipping Wt. Lbs. (kilos) (approx.): 4500 (2025)
Outline Dimensions
Height: inches (mm): 68" (1727.20)
Width: inches (mm): 56" (1422.40)
Depth: inches (mm): 52" (1320.80)
Feeder-Stainless Steel (all vibratory): included
WT-1500
Die Requirement: 1500" or "0”
Screw Dia. Capacity: #2 to 1/4" (6.35)
Blank Length: inches (mm): Up to 3" (76.20)
Speed Range: 90 to 700 ppm
Die Pocket Depth: inches (mm): 3" (76.20)
Main Motor Drive: HP NC (kw): 10 HP A/C (7.0)
Electrical: 230 V/3PH/60 Cycles
Shipping Wt. Lbs. (kilos) (approx.): 5500 (2475)
Outline Dimensions
Height: inches (mm): 73" (1854.20)
Width: inches (mm): 81" (2057.40)
Depth: inches (mm): 60" (1524)
Feeder-Stainless Steel (all vibratory): included
* Variable frequency motors
** Outside tooled
Standard thread rolling practice applies when rolling maximum part diameters and lengths.
WARREN THREAD ROLLER SPECIFICATIONS
WT-10, WT-20, WT-30
WT-10B
Die Requirement: 10 or 1015
Screw Dia. Capacity: #6 to 5/16" (7.93)
Blank Length: inches (mm): Up to 4" (101.60)
Speed Range: 80 to 400 ppm
Die Pocket Depth: inches (mm): 4-1/8" (104.77)
Main Motor Drive: HP NC (kw): 20 HP A/C (14.0)
Electrical: 230 V/3PH/60 Cycles
Shipping Wt. Lbs. (kilos) (approx.): 7500 (3375)
Outline Dimensions
Height: inches (mm): 83" (2108.20)
Width: inches (mm): 90" (2286)
Depth: inches (mm): 70" (1778)
Feeder-Stainless Steel (all vibratory): included
WT-10
Die Requirement: 10 or 1015
Screw Dia. Capacity: #6 to 5/16" (7.93)
Blank Length: inches (mm): Up to 6" (152.40)
Speed Range: Up to 500 ppm
Die Pocket Depth: inches (mm): 6" (152.40)
Main Motor Drive: HP NC (kw): 30 HP A/C* (21.0)
Electrical: 460 V/3PH/60 Cycles
Shipping Wt. Lbs. (kilos) (approx.): 12300 (5535)
Outline Dimensions: -
Height: inches (mm) 80" (2032)
Width: inches (mm): 90" (2286)
Depth: inches (mm): 104" (2641.60)
Feeder-Stainless Steel (all vibratory): included**
WT-20
Die Requirement: 20 or 10
Screw Dia. Capacity: #6 to 3/8" (9.52)
Blank Length: inches (mm): Up to 6" (152.40)
Speed Range: Up to 350 ppm
Die Pocket Depth: inches (mm): 6" (152.40)
Main Motor Drive: HP NC (kw): 30 HP A/C* (21.0)
Electrical: 460 V/3PH/60 Cycles
Shipping Wt. Lbs. (kilos) (approx.): 13000 (5850)
Outline Dimensions: -
Height: inches (mm) 80" (2032)
Width: inches (mm): 90" (2286)
Depth: inches (mm): 104" (2641.60)
Feeder-Stainless Steel (all vibratory): included**
WT-30
Die Requirement: 30 or 20
Screw Dia. Capacity: #6 to 1/2" (12.70)
Blank Length: inches (mm): Up to 6" (152.40)
Speed Range: Up to 250 ppm
Die Pocket Depth: inches (mm): 6" (152.40)
Main Motor Drive: HP NC (kw): 30 HP A/C* (21.0)
Electrical: 460 V/3PH/60 Cycles
Shipping Wt. Lbs. (kilos) (approx.): 13000 (5850)
Outline Dimensions
Height: inches (mm): 80" (2032)
Width: inches (mm): 90" (2286)
Depth: inches (mm): 104" (2641.60)
Feeder-Stainless Steel (all vibratory): included**
* Variable frequency motors
** Outside tooled
Standard thread rolling practice applies when rolling maximum part diameters and lengths.
HIGH-SPEED ASSEMBLER FOR SEMS
Model WT-1000/WT-1500 Warren thread rollers coupled with the Warren-Linread Model BW-2400 Assembler provides reliable, high-speed assembly of a wide variety of screw (or bolt) and washer combinations in one efficient, space-saving package.
This system provides total adjustability for reducing setup time. The integral 21" vibratory screw blank feeder has fully adjustable feed rails to provide maximum versatility and speed. Setup is accomplished quickly and requires only the adjustment of the screw blank fingers and the washer feed disc. If the screw blank diameter doesn't change, then you only change the washer feed disc.
SPECIFICATIONS:- 24-station rotary turret assembly
- Washer feed system – vibratory
- Size range – screw diameter no. 4 through 5/16" (M3 thru M8)
- Screw length from 1/4" thru 1-1/4" (6mm thru 30mm)
- Production speed is infinitely variable up to 500 units per minute, depending on washer type
- Maximum washer diameter – 3/4" (19.05mm)
- Standard electric's 115V, 60CY, 3PH
- No washer – no blank sensor is standard
A COMPLETE LINE OF PART FEED EQUIPMENT FOR A TOTAL TURNKEY SYSTEM
We offer the industry's broadest range of standard and custom engineered part feeding equipment and systems for use with Warren thread forming equipment.
OUR INTEGRATED SYSTEMS CAN BE DESIGNED TO INCLUDE:
- Vibratory feeder bowls
- Linear feed systems
- Special thread rolling applications
- Bolt-on rail extensions for increased feed rail capacity
- Interchangeable die cartridges for presetting dies
- Above-rail thread rolling capabilities
- Tube feeders
- Parts sorters
- Parts loaders
- Sound enclosures